Bamboo bending techniques: creating curved masterpieces
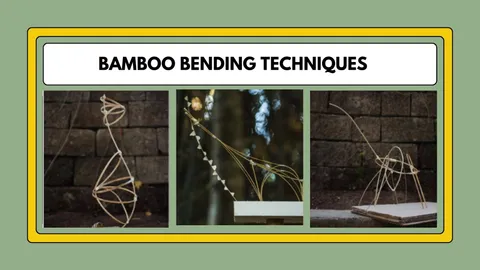
Bamboo has long served as a symbol of natural resilience and flexibility, prized for its versatility in various crafts and structural applications. As a material, it possesses an unparalleled combination of strength and pliability, making it an ideal candidate for crafting curved masterpieces. The art of bending bamboo explores these properties, allowing designers and artisans to shape its elegant forms into awe-inspiring structures and intricate designs. Through techniques ranging from traditional to innovative, bamboo bending not only highlights the material's innate beauty but also extends its utility in sustainable building practices and artistic expressions. This article will delve into the essentials of bamboo bending, exploring its flexibility characteristics, bending techniques, tools, and safety measures, along with applications in architectural designs and decorative elements.
=======================================================
Understanding bamboo flexibility
Bamboo's flexibility stems from its unique structural composition, which consists of vascular bundles, fibers, and parenchyma cells, enabling it to bend without breaking. When compared to other materials like wood, bamboo acts as a functionally graded material (FGM), with variations in density and fiber arrangement along its cross-section. This grading allows bamboo to exhibit both rigidity and flexibility as needed, depending on the load's orientation. Understanding these characteristics is crucial for effective bending techniques, such as steaming and soaking, which help shape bamboo into desired curves while preserving its integrity. Such adaptability is not only essential for crafting furniture and architectural elements but also fosters innovative design approaches. Thus, mastering bamboo's flexibility and applying the right techniques can lead to the creation of visually striking and structurally sound curved designs.
Characteristics of bamboo for bending
Structural Composition: Bamboo features a unique combination of components vascular bundles, cellulose fibers, and parenchyma cells arranged in a way that grants flexibility without compromising its strength. The outer layers pack tightly with fibers that offer tensile strength, while the softer parenchyma cells inside absorb energy and provide a cushioning effect during bending. This sequence is comparable to a well-crafted orchestra, where each instrument contributes its part, creating a harmonious composition of resilience and malleability.
Hollow Structure: The hollow nature of bamboo stems reduces weight without compromising structural integrity, akin to a well-engineered bicycle frame that supports the rider's weight while allowing for agile maneuvers. This hollow cylindrical form is key to bending bamboo, as it permits the material to flex and absorb loads that might fracture denser materials.
Functionally Graded Material: Bamboo's variation in mechanical properties across its cross-section akin to a gradient of colors in a painting allows it to transition smoothly from a rigid exterior to a flexible interior. This functionally graded feature gives artisans the freedom to use bamboo in diverse applications, from sturdy beams to delicate sculptures.
Bending Techniques: Techniques such as steaming and soaking leverage bamboo’s inherent characteristics, softening it for reshaping while maintaining its robustness. These processes are crucial when designers aspire to transform rigid stalks into fluid architectural curves or organically shaped furniture pieces, just like crafting a masterpiece from a raw block of marble.
Factors affecting bamboo flexibility
Flexibility in bamboo is influenced by numerous factors, each comparable to the varied notes that make up a symphony, where precise attention to detail ensures a flawless performance. Significant factors include:
Species of Bamboo: Much like varieties of grapes producing distinct wines, different bamboo species yield varying flexibility levels. Species such as the Dendrocalamus asper are celebrated for their pliability, making them perfect for structural bends in construction.
Age of Bamboo: Youthful bamboo displays an inherent pliability, like a sapling swayed by the wind, as opposed to older, denser stalks which provide more resistance to deformation. Therefore, harvesting bamboo at an optimum age can enhance its bending capability.
Moisture Content: Moisture acts like a lubricant among bamboo fibers, easing their movement against each other. Fresh bamboo boasts high moisture levels akin to a sponge freshly soaked with water, allowing easier manipulation and reducing fracture risk.
Temperature and Treatment: Exposing bamboo to heat conditions similar to a sauna session for muscles increases fiber flexibility. Methods like steaming or boiling prior to bending modify bamboo's internal structure, facilitating a seamless reconfiguration.
Techniques for bending bamboo
Bending bamboo taps into a delicate balance between force and finesse, much akin to the act of molding clay to a potter. Choosing the right bending technique depends on the desired outcome, each method serving as a specific tool for the artist’s vision. Soaking, steaming, and direct heat application techniques are instrumental in transforming rigid bamboo rods into graceful arcs, embracing both traditional wisdom and modern innovation. This section will take you through the nuances of these techniques, discussing how they optimize bamboo's flexibility to create resilient and aesthetically pleasing curves.
Soaking method for flexible bends
To embrace the soaking method is akin to mastering the gentle art of persuasion, coaxing bamboo into compliance through patience and understanding. This technique elevates bamboo's pliability and renders it amenable to bending:
Preparation: Green bamboo, fresh from its harvest, is like a newborn eager to explore flexibility, presenting a malleable state ideal for bending. Selecting and preparing these green poles set the foundation for successful manipulations.
Soaking Process: Submerging the bamboo in water becomes a ritual where both time and temperature are critical, much like marinating a fine cut of steak to achieve the perfect flavor. The rule of thumb involves a minimum 24-hour immersion, softening fibers and permitting more graceful curves.
Gently bending and drying the moistened bamboo completes this gradual transformation, fixing its newly acquired shape without undue risk of breakage. This method, while time-consuming, is indispensable for achieving subtle bends in bamboo creations.
Heat bending techniques
Heat bending marries intensity with precision, transforming bamboo through the controlled application of warmth, like developing a photograph in a darkroom.
Heating Method: Boiling water, steam, or infrared heat sources work as meticulous agents, seizing and channeling heat to transform rigid bamboo into an elastic wonder. Each method serves a calculated purpose, whether bathing bamboo in steam for thorough fiber penetration or targeting specific areas with a heat gun or torch.
Heat Application: Understanding how heat flows across bamboo is akin to conducting an orchestra, ensuring each section gains enough exposure without tipping into decay. Steaming chambers, careful flame passes, or immersion methods involve calculated timing, avoiding scorching while achieving necessary fiber softening.
Upon achieving pliability, bending follows, guided by steady hands and calm assurance, using clamps to secure and mold until cooling sets the final form. As with fine wine, heat bending requires patience and balance, leading bamboo into an elegant dance of resilience and artistry.
Steam bending process
The steam bending process transforms bamboo into an obedient medium, reshaped under vaporous whispers reminiscent of ancient crafts sustained through generations. This method demands precision in planning, execution, and monitoring:
Preparing the Steam Chamber: Choices of structure are manifold, often involving a combination of metals, woods, and heat-proof materials. A well-constructed chamber performs as a seal, containing and directing steam to embrace bamboo in warmth.
Soaking: Soaking prior to steam immersion acts as a preliminary stress relief treatment. It conditions the bamboo for the temperature shift, preventing shock to the fibers that may otherwise lead to failure.
By steaming bamboo for an appropriate duration (correlating to its thickness), artisans expand its flexibility momentarily until the desired shape coalesces. Under adept hands, molds guide these changes, securing bamboo with patience until its new form hardens. Such nuanced mastery elevates steam bending to an art form, allowing the creation of sweeping curves and bold designs.
Compression bending method
Compression bending encapsulates a blend of restrained power and subtle adjustments, akin to taming a wild river’s course without diminishing its flow. By applying controlled force, bamboo is persuaded into curves:
Bending Form Selection: The maestro starts with selecting robust templates, where even pressure makes for smooth, even curves. These molds are precise instruments, matching desired shapes and accommodating structural constraints.
Graduated Pressure Application: Gradual pressure, akin to nurturing a young sapling, encourages bamboo to conform without straining its fibers beyond their capacity. Clamps or straps ensure even distribution, retaining the integrity of the structure.
The art of compression bending lies in its patience, allowing ample time for the bamboo to set into its revised form. As it reclaims its rigidity amidst the curves, the bamboo asserts its resilience once more, standing testament to the artist’s balanced approach between force and gentleness.
Tools and equipment for bamboo bending
Achieving mastery in bamboo bending relies heavily on a symphony of specialized tools and equipment designed to finesse and craft bamboo’s versatile forms. These instruments are akin to the brush and palette in the artist’s hands, instrumental in shaping bamboo into desired silhouettes. From steam generators and heat guns to bending jigs, each piece plays a pivotal role in ensuring that bamboo is coaxed into compliance with precision and efficiency. A craftsman’s toolkit must be well-stocked and finely tuned, balancing technology with tradition. Through a nuanced understanding of these tools, artisans can unlock the secrets of bamboo, taking the raw, untamed stalks and transforming them into iconic structures and designs.
Essential tools for heat bending
In the realm of heat bending, the right tools can elevate one’s craft from mere functionality to fine art. Each tool aligns to deliver heat intelligently, grasping control and precision akin to a conductor orchestrating a symphony.
Steam Generator: A staple for those utilizing steam to induce flexibility, these generators serve as industrious engines producing hot vapor necessary for softening bamboo fibers. Conveniently portable units or large, industrial models offer a range of options based on project size.
Heat Gun or Butane Torch: Precision is key, as these tools apply targeted heat to smaller sections, facilitating intricate projects needing calculated and definite adjustments.
Boiling Water Setup: Traditional and consistent, boiling water systems submerge perforated sections of bamboo, offering uniform warmth suited for medium to larger-scale projects.
Clamps and Weights: To maintain form through the cooling stages, these securing items brace bamboo, cementing new shapes into permanent contours.
Each instrument is wielded with intention and care, merging modern ingenuity with age-old craftsmanship. In capable hands, these tools lend a critical edge, ensuring that every bend and curve respects bamboo’s sophisticated balance of strength and grace.
Creating a steam chamber for bending
Creating an effective steam chamber involves envisioning a pressurized space that envelops the bamboo in controlled warmth. It must be an efficient cocoon where heat converges, enhancing pliability and facilitating serene transitions into new forms.
Steam Chamber Structure: Varieties in materials (PVC pipes, metal-clad chambers, or robust wood constructions) provide flexibility, serving as core elements in crafting a chamber capable of sustaining steam’s delicate force.
Heating Source: Precision heaters or stovetop elements ensure a reliable steam supply, vital in demystifying stiffness and rigidity. Consistency here compliments the entire process, ensuring steam saturation naturally radiates throughout.
PVC’s versatility shines in crafting adaptable chambers; capped ends create effective steam environments when paired with kettle steam connections. However, maintaining a meticulous seal during chamber construction prevents valuable vapor loss.
Bamboo’s pre-treatment, via soaking, further aids in opening fibers to impending steam baths, serene in their unification of fiber looseness and controlled pressure application. Such harmony results in bamboo more readily adopting curves, crucial for ensuring structural integrity and alluring aesthetics post-bend.
Using bamboo bending jigs
Bending jigs serve as dynamic templates, guiding and holding bamboo as it finds its newly intended form. These constructs are indispensable, offering structural resilience and continuity when molding bamboo around desired contours.
Types of Jigs: Material choices range from supple woods to fortified metals, each tailored to complement the desired curvature of bamboo and withstand pressure while securing it.
Construction and Use: Careful alignment with existing frameworks ensures that each jig matches precision requirements. The process involves immediate placement of steamed bamboo into these configurations for cooling and setting, facilitated by clamps and tailored restraints.
During cooling, bamboo remains fastened within the jig to achieve a clean, bend-conformed surface, stabilizing the new shape over time. These specialized frameworks amplify bamboo’s inherent potential, allowing craftsmen to explore the boundaries of creativity in architecture and decorative applications with each painstakingly orchestrated curve.
Structural considerations in bamboo bending
Understanding the structural aspects of bamboo bending reveals an intricate dance between material constraints and creative possibilities. Important considerations include calculating the moment of inertia an engineering factor dictating bamboo’s competence in assuming curves and managing load-bearing responsibilities. Leveraging bamboo’s material adaptability empowers designers to embrace aesthetically daring shapes and new structural paradigms confidently. Exploring these considerations not only contributes to crafting beautiful designs but ensures functionality and safety in applications ranging from architectural frameworks to interior innovations, positioning bamboo as a forerunner in sustainable building practices.
Moment of inertia in bamboo structures
The moment of inertia, a fundamental component of engineering calculations, quantifies a section’s ability to resist bending. With bamboo, often modeled for its elliptical cross-section, attention to detail here reveals significant insights:
Cross-Section Analysis: Bamboo’s unique, hollow cylindrical structure emphasizes variations in structural responses compared to materials like wood. These influences mean that solutions considering bamboo’s elliptical forms tend to be more accurate in bending where precise control is required.
Strength Ratios: Effective use involves understanding maximum stress points, usually located at outer fiber extremes, using realistic assumptions over force and stress distribution. This is crucial for validating theoretical models built on approximations or simulations.
The structural advantage of bamboo, akin to mastering a musical instrument, demands precision and harmony in understanding moment of inertia, facilitating superior designs ready to accept modern load demands akin to traditional structures reimagined with contemporary flair.
Load-bearing capabilities of bent bamboo
Bamboo, in its bent form, unveils enhanced mechanical properties with numerous applications extending into innovative construction and design spheres. Understanding these properties enables exploitation of bamboo’s load-bearing potential:
Mechanical Insights: As a lightweight yet robust material, bamboo in bent configurations achieves superior performance ratios, ideal for economically resilient building applications. This characteristic is prominent in modern green designs where efficiency and sustainability merge.
Bending Techniques: Employing proven bending processes conserves bamboo’s junctional integrity while yielding flexible yet strong configurations. Mastery of this process provides avenues for integrating bamboo in complex arrangements, from canopies and bridges to nationally recognized sustainable development projects.
Such applications emphasize bamboo’s inherent capabilities alongside humanity’s relentless drive for environmentally-friendly and beautiful building solutions. They demonstrate that the understanding and artful application of bamboo’s unique features can transform visions into viable, impactful realities.
Applications of bent bamboo
Bent bamboo’s applications are as diverse as they are innovative. From structural elements in architecture to sophisticated furniture designs and ornamental displays, the versatility of bamboo demonstrates incredible potential for creative expression and sustainable solutions. By reshaping bamboo into curves, practitioners unlock new possibilities, generating a marriage of strength, beauty, and environmental consciousness inherent to bamboo’s core. As awareness grows around sustainable materials, bent bamboo stands to significantly impact design, contributing to initiatives that prioritize the planet without sacrificing aesthetic or functional standards.
Architectural structures using curved bamboo
In architectural spheres, curved bamboo constitutes an inventive approach amalgamating tradition with avant-garde implementations, addressing both form and function:
Techniques and Structures: Structural techniques such as Rup Rup and Lidi Bundles leverage bamboo’s natural complements to assemble cutting-edge constructions. These methodologies deliver precision assembly, creating essential structural features like arches or expansive canopies.
Diverse Applications: Curved bamboo has unfolded in projects that integrate hyperbolic paraboloids or spatial gridshells, demonstrating bamboo’s capacity and elegance when paired with balanced engineering. In doing so, bamboo establishes itself as a feasible alternative in architectural landscapes where organic shapes encounter the practical rigors of construction.
These projects foster the acceptance of bamboo comprehensively, utilizing computational insights and traditional methodologies to create accessible, inspiring spaces that harmonize with and celebrate the natural world.
Furniture design with bent bamboo
Bent bamboo in furniture design amplifies characteristics of grace and functionality, presenting nature and utility to create modern solutions connected by old and new practices:
Design Techniques: Heating, pressuring, and strategic notch-cutting have paved the way for bamboo’s application in ergonomic and stylistically appealing furniture. These techniques imbue everyday objects like chairs and tables with flexibility, comfort, and endurance.
Functional Aesthetics: As a material choice, bamboo exudes aesthetic coolness coupled with steadfast capability, offering elegant forms enriched by structural performance, showcasing comfort and artistic vision reflected in furniture objects.
Decorative elements and art installations
Bent bamboo happens to embody remarkable artistry when integrated within decorative spheres, whether for private enjoyment or public installation:
Decorative Features: Utilizing curved bamboo enhances capabilities for creating attractive accents in spaces, gardens, and furniture arrangements evoking harmony with nature while crafting engaging environments charged with organic vitality.
Artistic Installations: Art drawn from bamboo derives its appeal not only from ecological consciousness but by promoting imaginative expression. Through installations displaying forms driven by intent and creativity, artisans capture fleeting moments, transforming environmental beauty into permanent fixtures within the landscape.
These applications celebrate bamboo’s resilience and adaptability, cemented within decorative contexts where design ideals converge with sustainable philosophies confidently.
Safety precautions in bamboo bending
Despite bamboo's allure and versatility, safety remains paramount during bending processes. Appropriate precautions assure the craftsman’s protection while optimizing bamboo’s potential within design contexts. From protective gear to organized work environments, a disciplined adherence to safety measures must become second nature for those seeking success in manipulating bamboo’s capabilities safely, unveiling limitless design possibilities while safeguarding one’s health and well-being.
Protective gear for bamboo bending
Preparedness begins with adequate protective gear, forming an essential layer between the artisan and unforeseen hazards:
- Consistent Usage: Quality gloves, safety glasses, dust masks, and ear protection create necessary barriers, facilitating efforts while preventing injury from splinters, debris, or unexpected mishaps encountered throughout the process.
Workspace setup for safe bending
In equally maintaining effective practices, the workspace must stand organized and conducive to clear, precise efforts:
- Orderliness: Ensuring clear, ventilated, and well-lit spaces fosters productivity unhindered by potential clutter or ambivalence, securing clear efforts aimed at achieving the perfect bend.
- Stable Work Surfaces: Stability in workbenches and tools reduces unpredictable variables within operations, allowing for quality craftsmanship unmarred by imbalanced results or subsequent safety hazards.
Being able to safely and effectively navigate the intricate world of bamboo bending requires vigilance and competence. Together with practice, these elements ensure that the art of crafting curved masterpieces remains rewarding and adventurous.
Challenges and solutions in bamboo bending
Navigating the complexities inherent in bamboo bending requires practitioners to ascertain and mitigate associated challenges, ensuring craftsmanship attains both vision and precision unbeheld by errors. Effective solutions arise through understanding common pitfalls and applying corrective practices. Knowledge of these contributes to unleashing creativity, transforming problems into opportunities for imitation and innovation.
Common pitfalls when bending bamboo
Bamboo bending, be it due to natural imperfections or handling misjudgments, may succumb to various pitfalls present throughout the process. Addressing these involves recognizing and rectifying the root causes of failure:
- Material Shortcomings: Misalignment in anticipated moisture levels, species selection, or preparation timing can inhibit bending processes.
- Safety Negligence: Transformative processes require comprehensive safety commitments, guarding against sudden or debilitating accidents.
- Bending Oversights: Throughout execution, errors often manifest through the misapplication of force, temperature, or tools, risking both personal and structural disaster.
Recognizing these pitfalls unlocks better practices, emphasizing precision and focus in approach while bypassing such misjudgments in future projects.
Repair techniques for damaged bamboo
Comprehension becomes a core facet in damage management and renewed efforts in bamboo development:
- Reinforcement and Repair: When damaged, solutions include epoxy adhesives, bamboo splints, or doweling, each paired with mechanical reinforcement methods.
- Heating and Reshaping: Deformities benefit from controlled reheating or steam applications, encouraging adjustments that correct form and maintain integrity.
Embarking on repair animations showcases expertise and innovation, offering reclaimed satisfaction in bamboo mastered anew through corrective insights acquired in practice.
Advanced techniques and innovations
While traditional methods persist, advancements in bamboo bending continue to redefine possibilities. Integrating technology and artistry, practitioners elicit new creative scopes, navigating visionary compromises offered by complex geometries.
Exploring new technologies in bamboo bending
As technology intersects with industrious assent, practitioners enlist digital and mechanized tools to explore sophisticated ideas:
- Digital Design and Modeling: Utilizing simulation software for visualizing possibilities before engagement exemplifies technology's role in shaping expectations within reality. Such insight promotes efficiency alongside captivating ambition.
- Laminated and Composite Applications: Beyond temporality, advancements include laminate sequences reinforced by composite materials, overcoming traditional limitations in both dimension and durability.
These techniques deploy ingenuity with tangible that fosters appreciation and expanded utilization amid contemporary crafts.
Case studies of curved bamboo masterpieces
Displaying achievements in contemporary symbiosis of structural form and artistic function:
- Sculpture and Environmental Attractions: Artistries conveyed through renowned case studies demonstrate bamboo’s versatility within lifetime-defining works ranging from sustainable architecture coveted globally to ephemeral art capturing emotional connections between structure and nature.
- Dependable Collaborations: Constructions like SUP Atelier’s Swirling Cloud Pavilion embrace bamboo through integration. In this, balance and creativity dissolved formality, immortalizing creativity as bamboo triumphs across applications.
Through these explorations, bamboo ascends beyond mere resource a muse cemented within art and architecture itself showcasing horizonless potential still awaiting discovery.