Rattan Cutting Techniques: Precision in Handicraft Production
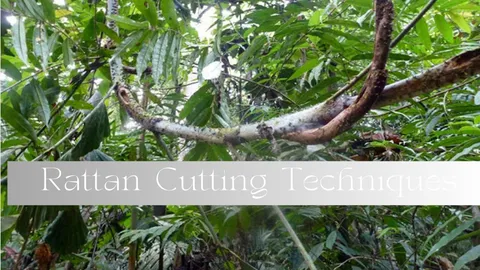
In the realm of handicraft production, rattan emerges as a versatile material celebrated for its combination of durability and aesthetic appeal. But amidst this celebration lies a crucial foundation precision in rattan cutting. This seemingly humble step holds the power to transform raw rattan into works of art, influencing not only the craftsmanship quality but also the material's very integrity. As an artisan shapes, marks, and meticulously cuts each cane, they engage in a dance as old as time, building on traditions while embracing innovation. Whether through careful manual methods that echo with the humanity of handmade or the swift efficiencies offered by modern techniques, the nuances of rattan cutting reflect a blend of art and engineering. While the core of rattan cutting remains deeply tied to traditional practices, today’s landscape reveals a tapestry enriched by modern advancements. From hand-sawing and debarking to the precision of laser cutting, each technique offers unique possibilities and challenges. These methods not only speak to the technicalities of the craft but also weave stories of cultural heritage, economic implications, and the ever-pressing need for sustainable practices. In this detailed exploration, we delve into the myriad facets of rattan cutting techniques, their impacts on craftsmanship, and their evolving role in the modern world.
=============================================================
Understanding Rattan Cutting Techniques
Delving into the world of rattan cutting techniques unveils a captivating interplay between tradition and modernity. As we navigate this sphere, it becomes evident that while the process may seem straightforward, its implications are profound. Understanding the intricacies involved in these techniques can be likened to appreciating the craftsmanship of a painter whose strokes create not only a picture but a narrative, rich and full-bodied. Through key methods such as hand-sawing and debarking, alongside tools that facilitate precision like awls and reed cutters, artisans craft a symphony of structure and beauty. These methods and tools are akin to a dancer's partner, providing balance, rhythm, and finesse to the rattan's final form.
Central to this exploration is the importance of precision, driving home the point that every millimeter counts when translating rattan canes into exquisitely crafted pieces. Precision cutting not only enhances structural integrity and aesthetic appeal but also plays a role in boosting efficiency, thereby reducing waste and empowering artisans to focus their energies on innovation and design excellence. Intricacy, quality, and effectiveness dance hand-in-hand within these cutting techniques, transforming raw materials into timeless artisan expressions.
Key Methods in Rattan Cutting
The nuanced art of rattan cutting is shaped by an assortment of key methods that have been honed over generations, ensuring the material's optimal use in handicraft production. Each technique serves a distinct purpose, much like the notes of a symphony creating harmony.
Hand Sawing:
- Emphasizes control and precision, offering artisans an intimate connection with the material. Ideal for intricate works where every curve matters.
- Traditional yet irreplaceable, hand sawing stands as a testament to handmade craftsmanship, promoting attention to detail that machines struggle to replicate.
Power Tools:
- Power tools such as saws and cutters significantly reduce labor time, enhancing efficiency in commercial production settings.
- While these tools offer speed, they must be wielded with skill to prevent compromising the cane's structural integrity, akin to wielding an instrument that, though capable of great volumes, must be expertly controlled to avoid discord.
Debarking and Trimming:
- Following the primary cut, debarking sheds the protective outer layer, preparing the rattan for bending and coating processes.
- This technique is crucial for achieving a refined finish, akin to removing impurities to reveal the pristine core of a gemstone, ensuring durability and aesthetic appeal.
Soaking and Conditioning:
- A preparation step often involving soaking rattan to increase pliability, rendering it suitable for weaving and intricate manipulations.
- By conditioning the material, artisans ensure it flexes under stress without breaking, akin to a dancer warming up before a performance.
Precision is the guiding principle across these methods, ensuring the rattan preserves its natural beauty while meeting the demands of modern craftsmanship. The journey from raw material to refined product requires a careful balance of tradition, skill, and innovation to achieve the highest quality outcomes.
Tools Required for Precision Cutting
Precision in rattan cutting is as much about the right tools as it is about the right techniques. The tools serve as extensions of the artisan’s hand, each designed to complement the meticulous requirements of rattan crafting a ballet of interaction wherein every tool has a role to play.
Rattan Cutters:
- Tailored for rattan, these cutters offer the delicate touch needed to slice through fibers without fraying, providing clean, crisp edges.
- Crafted to suit the material’s unique characteristics, their ergonomic design mirrors a tool in an artist’s hand smooth, precise, purposeful.
Sharp Knives and Scissors:
- Perfect for detailed work, these sharp implements facilitate intricate cuts and shapes, integral in the fashioning of seamless designs.
- Much like a sculptor’s chisel, these tools enable artisans to carve beauty from simplicity, shaping the inanimate into purposeful form.
Reed Cutters:
- Expertly engineered for precision and control, these tools slice through reeds with exceptional accuracy, allowing for minute adjustments.
- In artistry often marked by finesse, reed cutters empower the craftsman to create not just objects, but experiences meant to be seen and felt.
Awls and Spoke Weights:
- Awls craft holes with precision, wherein each puncture is deliberate, guided, and tailored to accommodate intricate woven designs.
- Spoke weights maintain balance during cutting, ensuring stability and alignment akin to a maestro’s baton cuing harmony amongst instruments.
Together, these tools enable artisans to navigate the delicate nuances of rattan, transforming raw potential into refined possibilities. The dance between material and instrument marks the heart of craftsmanship, where every cut is a note, and every finished piece, a composition.
Importance of Precision in Rattan Craftsmanship
Precision in cutting is the cornerstone of rattan craftsmanship, underpinning the elegance and durability of every creation. This deliberate attention to detail ensures that each cut is not just about separation but about opportunity a precise opening to craft something magnificent.
Structural Integrity:
- Every cut or slice must maintain the rattan's inherent strength, supporting the integrity of the end piece. Precision aligns with function, much like tailored seams hold a garment together.
- It is the assurance that craftsmanship will stand the test of time, echoing the artisan's unwavering commitment to quality.
Aesthetic Appeal:
- Flawless edges and smooth joins elevate an item from the mundane to the exquisite, capturing attention and inciting admiration.
- Precise cuts are the unseen brush strokes on a canvas where beauty and precision become synonymous, bestowing artfulness upon functionality.
Efficiency and Waste Reduction:
- Precision minimizes material wastage as every piece cut fits purpose and design, reducing unnecessary rework or scrap.
- This efficiency mirrors the calculated steps in a dance, where nothing is left to chance, optimizing resources at every turn.
Facilitating Intricate Designs:
- The grace and intricacy of woven patterns rely on the minute precision of cuts.
- Each rattan strand finds its place, much like a puzzle piece, in a design that reflects advanced techniques and elemental creativity.
This commitment to precision is at the core of all masterful rattan works, enhancing the artisan's capabilities and elevating the industry’s standards. For in precision lies the promise of longevity and the whispers of tradition lovingly upheld.
Comparison of Rattan Cutting Techniques
The juxtaposition of traditional and modern cutting techniques in rattan craftsmanship is emblematic of the broader dialogue between past and present. Each method embodies unique strengths and areas for improvement, influencing efficiency, quality, sustainability, and innovation. Traditional hand-cutting techniques symbolize personal touch, rich heritage, and bespoke artisanship. They preserve cultural nuances and articulate craftsmanship through deliberate, patient labor qualities that are increasingly rarer yet deeply valued in the craft world. However, these methods can be arduous and restrictive in meeting large-scale production demands.
Conversely, modern techniques bring machinery and technology into play, unveiling new potential for speed and consistency. Electric and laser tools provide the velocity needed to cope with upscaled production while promising economically viable output without compromising base quality. Yet, such approaches occasionally fall short of the subtleties and artistry inherent in traditional methods.
Ultimately, the choice between tradition and modernity is a balance between speed, precision, customization, and environmental considerations. Techniques evolve with market demands, merging artisanship with industrial innovation. In this rapidly changing environment, each approach provides tools that cater to the diverse needs within the rattan market, lending diverse storytelling opportunities within its manufacture.
Traditional vs. Modern Cutting Techniques
In the realm of rattan craftsmanship, the divergence between traditional and modern cutting techniques is not merely a matter of method but an illustration of evolving values and capabilities. Just as a painter's tools extend from charcoal to the airbrush, so too do rattan artisans select their implements, shaping the narrative of their trade through the techniques they employ.
Traditional Cutting Techniques:
- Predominantly employ hand tools knives and single-blade cutting implements which afford artisans significant control over the process.
- Promote intricacy and customization, each product reflecting a unique, artisanal quality.
- Imbue products with uniqueness, yet these methods are inherently more time-consuming and labor-intensive, limiting their applicability to large-scale production.
Modern Cutting Techniques:
- Leverage machinery, such as electric cutting machines, radically enhancing speed and efficiency.
- Provide speed and volume, often at the expense of detailed craftsmanship inherent in traditional methods.
- Present precision challenges, where machinery struggles with the nuanced handling required for certain elaborately woven rattan designs.
This comparison not only underscores the strengths but also highlights the distinct limitations each technique encounters:
- Efficiency: Machines boast far brisker production times, essential for commercial gain, whereas traditional methods excel in rendering superior craftsmanship.
- Work Quality: Handcrafted uniqueness versus the uniform high-quality consistency found in machine cuts.
- Adaptability: Traditional artisans are nimble, easily tweaking methods for new designs; machine production often requires pre-set configurations.
The choice between traditional and modern techniques rests on aligning production goals with market positioning, balancing speed and customization skills. Each technique, a testament to the adaptability of crafting methods, must evolve to harmonize with the technological advancements altering rattan production's landscape.
Effects of Cutting Techniques on Quality
The implications of cutting techniques on the quality of rattan products are far-reaching, with each methodological choice shaping not just the physical outcome but the very narrative thread of craftsmanship and production efficiency. The approach to cutting, akin to an artist’s selection of medium, determines texture, strength, and the ultimate potential of the material a delicate dance that defines success or quietly undo it.
Precision Matters:
- Methods involving careful manual techniques often yield superior-quality rattan suitable for fine handicraft production. The precise cuts maintain tensile strength and structural integrity, vital for producing durable, high-value items.
- Conversely, mechanical approaches, through they offer efficiency, can compromise fibers, initiating splintering or uneven lengths, which affects the usability and longevity of resulting products.
Balancing Cost with Quality:
- Manual precision cutting is labor-intensive, reflecting higher production costs that may translate into premium product pricing justified by exceptional craftsmanship and minimal waste.
- Mechanical cutting, while cost-effective in reducing labor, risks higher waste levels from compromised canes, thus balancing savings with potential losses due to reduced product quality.
Industrial Impacts and Innovations:
- Innovative techniques prioritizing precision are vital for industry sustainability and competitiveness. For example, incorporating training modules and enhanced tools can reduce material waste while improving overall quality.
- This synergistic adherence to precision is not even a cost consideration as much as it is an investment in future viability and consumer satisfaction.
In this nuanced interplay, rattan craftsmen and producers navigate the critical relationship between cutting techniques and quality assurance. Their choices resonate through every product, embodying a commitment to excellence that honors tradition, endures over time, and evolves with necessity.
Cost Implications of Different Cutting Approaches
In the interwoven matrix of rattan production, the choice of cutting technique entails profound cost implications, influencing both economic viability and the caliber of the resulting products. The economic landscape of rattan craftsmanship is a complex choreography of budget management, resource allocation, and adherence to quality a dance of numbers and craftsmanship reflecting an unwavering commitment to excellence.
Labor Costs:
- Manual Cutting: Amplified labor intensity correlates with increased production costs, demanding skilled artisans who can uphold precision while maintaining the artistry involved in handcrafted items.
- Mechanical Cutting: Economically attractive due to reduced direct labor input, albeit tempered by potential quality-related expenses, as machines may require remedial clipping or adjustments post-cutting.
Material Waste:
- Precision Methods: Prioritizing manual techniques optimizes material utilization, minimizing waste, aligning with sustainability goals while ensuring every rattan strand finds its purpose.
- Mechanical Methods: Risk of higher wastage levels through misalignment or overcutting, where excess trimming becomes necessary, reflecting an inflexible facet of industrial cutting’s economy.
Balance and Decision-Making:
- Producers must weigh between initial investments in skilled labor and the potential returns from high-quality goods, which could command higher market prices.
- Incorporating innovative tools promoting precision can harmonize these costs, creating a cyclical benefit stream that reduces waste and enhances product desirability, thus increasing market competitiveness.
These financial considerations craft a narrative beyond the mere act of cutting; they encapsulate strategic investments and reveal the transparent interconnectedness between cost-efficiency and craftsmanship in the rattan industry. The balancing act of economies outlines a landscape where admirably crafted products emerge from carefully executed, cost-aligned methodologies that shine in quality and design excellence.
Grouping Rattan Cutting Techniques by Application
Rattan cutting techniques can be categorized into a framework governed by the end-use applications and tailored by the properties of various rattan species. This approach aligns with the unique characteristics and seasonal considerations impacting the raw material through crafting stages. By grouping techniques according to application and material properties, artisans can elevate both craftsmanship and the material's inherent versatility.
Basic Rattan Harvesting Techniques:
- Techniques vary based on intended use and environmental conditions. Employing selective cutting ensures sustainable use while enhancing regrowth potential.
- Proper harvesting balances environmental needs with artisanal requirements, ensuring a continuous supply of quality materials, akin to nurturing an ecological legacy.
Cutting for Weaving:
- Preparatory steps include soaking for better flexibility, ensuring rattan is ready for manipulation without damage. This method is ideal for producing intricately designed items and durable furniture.
Cutting Techniques by Species:
- Recognizing individual species characteristics guides the specific cutting and preparation methods, optimizing quality output. This detailed attention mirrors an herbalist’s care in selecting plants for their properties an essential touch to ensure optimal outcomes and functionality.
In navigating these techniques with attention to material, environmental, and artistic needs, artisans affirm their role as custodians of both craft and sustainability. By aligning cutting approaches with application-specific demands, they cultivate a rich tapestry of interactions reflecting both reverence for tradition and adaptability in contemporary practices.
Techniques for Different Rattan Species
Diversity in the rattan species necessitates a keen awareness of each type's unique properties, allowing for a tailored approach in cutting and preparation that ensures optimal functionality and aesthetic outcomes. Each species, like a character in a vast narrative, brings its traits to the plot, contributing to the rich tapestry of rattan craftsmanship.
Harvesting and Processing:
- Calamus simplicifolius: Known for its flexibility, suitable for intricate decorative designs. Its processing involves careful splitting and trimming, optimizing its noted malleability for fine detailing in craft scenarios.
- C. yunnanensis: Valued for robust mechanical properties, requiring methodical cutting for structural use. Preparation adjusts for its tensile strength, making it ideal for furniture meant to withstand significant stress.
Material Properties:
- Recognizing the variances in elasticity, durability, and application utility informs cutting methodologies specifically tailored to each species, ensuring that every piece of rattan fulfills its highest potential within crafting processes akin to bespoke tailoring.
- Species selection impacts every stage, from raw material to finished product, much like selecting ingredients that align with a gourmand's recipe, ensuring flawless execution.
Craftsmen attuned to these species-specific methodologies are apprenticed in a discipline of botanical knowledge, where each cut, decision, and final form speaks to the nuanced understanding of nature's diversity. By adopting specialized techniques, artisans expand creative frontiers and amplify the sustainable use of this wondrous resource.
Cutting Techniques for Various End Products
Rattan extends its versatile nature into a multitude of end products, engaging craftspersons to employ cutting techniques refined in both creativity and precision. Each product yields end-user requirements that shape cutting methodologies, ensuring that the journey from rattan cane to finished item produces pieces that are not only functional but stylistic narratives in their own right.
Furniture:
- Employs precise stem peeling and slicing into uniform lengths, maintaining consistency across all construction components. Structural integrity and aesthetic appeal rest upon how each cut aligns within the overall design, ensuring cohesion and durability.
Craft and Handicraft:
- Requires refined cutting of fine and intricate shapes destined for weaving or composites. Techniques emphasize splitting, smoothing, and trimming various widths, facilitating artistic expressions in woven crafts or cultural items.
Home Decor:
- Engages creative interface with angled cuts for intricate designs often used in decorative accents. Techniques vary, with hand tools and occasionally power tools employed for complex structuring.
Architectural Elements:
- Rattan cut and prepped for use in frameworks or decorative panels within designs where functionality mirrors sheer artistic statement. Construction applications may utilize robust patterns, meshes, or open weaving, all balancing form with function.
Each end product application demands an artist’s eye, a craftsman’s touch, and a strategist’s foresight, where precision techniques evolve under the umbrella of creative revelation without sacrificing utility. These methodological practices embrace the integral symbiosis between purpose and artistry, grounding the legacy of rattan across varied industries.
Seasonal Considerations in Rattan Cutting
The influence of seasonal cycles on rattan cutting techniques is unambiguous, dictating not only when rattan is suitable for harvesting but determining the material outcomes and enhancement of its cutting efficacy. Viewing seasonal considerations as a metaphorical tide, artisans synchronize their crafting schedules to flow harmoniously with nature's rhythm, reflecting a deep understanding of natural and temporal influences on rattan’s character.
Dry Season Harvesting:
- Optimal when sap content is lower, making rattan Cane’s easier to handle and less prone to damage during transportation or storage, indispensable for furniture and larger craft pieces.
- Ensures sturdier material output, akin to a shoemaker choosing the finest leather for durability and finesse in their creations.
Wet Season Challenges:
- Elevated sap levels render material softer and potentially weaker, necessitating careful handling or choosing different cutting approaches to safeguard cane stability.
- Timing coincides with careful planning, much like agricultural cycles guide optimal planting and harvesting for premier yields.
Environmental Impact and Sustainability:
- Harvesting aligned with seasonal patterns aids in ensuring resource sustainability by respecting natural regrowth cycles, critical in balancing production needs with ecological stewardship for the future.
- Mere adaptation becomes transformation, whereby sustainability morphs from a byproduct to a celebrated goal.
In this symbiotic relationship with nature, artisans function at a confluence where tradition, environment, and material conditions inform craftsmanship practices, demonstrating respect, understanding and capability at every facet of crafting. The art of harnessing seasonal cycles ensures a resilient process that prioritizes both the quality of handicraft production and its sustainable continuity.
Best Practices for Effective Rattan Cutting
Navigating the nuances of rattan cutting demands an adherence to best practices that elevate technique to a fine art. Much like a conductor steering an orchestra through crescendos and symphonies, artisans must balance precision, safety, and tool maintenance to produce harmonious outcomes. Whether creating elaborate rattan furniture or intricately woven handicrafts, executing effective cutting practices beautifully sculpts intangible visions into tangible artistry. Familiarity with environmental conditions, such as moisture and temperature, further refines cutting tactics, ensuring a seamless transformation of raw rattan into captivating products.
In mastering these steps, artisans restrict waste and enhance productivity, guaranteeing high-quality finishes for even the most complex designs. Encompassing tool upkeep as a core element, artisans extend the lifespan of costly equipment while safeguarding performance integrity. The interweaving of these practices permits proficiency and sustained excellence, revealing the craftsman’s expertise in every cleft and contour of completed projects. Embodied within these practices is an ethos of respect for the material, for the craft, and for the artisan’s journey through tradition into innovation.
Step-by-step Guide to Precision Cutting
Cutting rattan with precision is an art that requires strategic planning and methodical execution akin to preparing a stage for a play. Each step in the process interlinks to ensure the smooth metamorphosis of raw material into fine craft, where every cut serves a purpose in the broader narrative of craftsmanship.
Pre-Cutting Preparation:
- Gather Tools: Use sharp, specific tools for cutting rattan, including knives, measuring tapes, and stable cutting surfaces. You seek precise instruments, tailored like each brush for a painter.
- Select Rattan: Only the best rattan, free from imperfections, set to creativity. Soaking ensures flexibility, preventing cracking during cuts a stage unto itself.
Mark and Measure:
- Measure Lengths: Accuracy is critical; mark and double-check. The rattan piece’s future integrity demands foresight akin to a strategist carefully plotting a path.
- Define Cut Lines: Align marks with design goals a compass in the creation journey.
Cutting Execution:
- Position Rattan: Steadily secure with clams for unyield warranty, offering breath to precision.
- Mindful Cutting: With care, guide the tool along the marked line. Even pressure, angled cuts, and attention mirror a craftsman’s commitment to their method.
Post-Cutting Refinement:
- Smooth Edges: Sandpaper partners the cut, refining any inconsistencies. This final touch enhances safety and visual appeal.
- Organize Remaining Material: Store unused pieces safely, away from harmful elements to retain their integrity.
Through this precise choreography, artisans craft a narrative of intention and beauty. Aligning every step with deliberate specificity, the mastery of rattan cutting unfolds, echoing a tale of celebrated craftsmanship and unwavering dedication to quality creation.
Safety Considerations in Rattan Cutting
Safety in the realm of rattan cutting is non-negotiable, serving as an invisible thread that secures the well-being of artisans amidst the pursuit of precision. Much like the diligent procedures backstage that ensure a flawless performance, safety measures guard against accidents that may hinder the craft’s enchanting production.
Essential Protective Gear:
- Gloves and Goggles: Guard fingers and eyes against cuts and debris. Safety extends a sanctuary, analogous to armor shielding a knight on a journey.
- Well-Lit Workspace: Enhance vision and minimize errors. Light unveils clarity in cutting paths, echoing insight and focus within creativity.
Secure Cutting Practices:
- Tool Maintenance: Ensure tools remain sharp and well-maintained. Sharp blades minimize the force needed and enhance control, where safety translates into confidence.
- Securing the Material: Utilize clamps; instability leads to imprecision and risk. A stable surface beckons detail, affording the skill to thrive.
Organize Workspace:
- Tidy Space: An organized workspace embodies order, reflecting the artisan's control over chaos. It guards against slips and mishaps.
Prioritizing these safety protocols confirms mastery, empowering artisans to create with assurance. It sustains both the craftsman’s welfare and the quality of the crafted pieces, reinforcing that each artistic endeavor should not compromise safety for creativity.
Maintenance of Cutting Tools for Optimal Performance
The care and maintenance of rattan cutting tools are integral to the artistry of craftsmanship, ensuring tools echo the hands that command them. Each blade and edge serves a purpose, much like a maestro’s baton, guiding harmonious performance with precision at its core.
Routine Care Routines:
- Regular Sharpening: Blades glide seamlessly with purpose. Sharp tools embody focus, akin to a poet’s pen you sharpened each point for impact.
- Clean After Use: Demands non-negotiable sap and debris hinder progress. Meticulous cleaning maintains form, removing residue that might dull, corrode, or degrade over time.
Tool Storage and Inspection:
- Proper Tool Storage: Dry places guard against rust. Encased in protection much akin to work of art safely shelved until it speaks again.
- Inspect for Damage: Routine checks unveil longevity. Replace dulled blades or those showing wear to avoid inconsistencies that mar precision.
Tool Lubrication:
- Lubricate Mechanisms: Facilitate smooth interplay. Lubrication becomes the lifeblood ensuring uninterrupted rhythm in your craftsmanship.
Implementing these structured maintenance steps highlights an unwavering commitment to both process and outcome, ensuring each tool’s role celebrates and enhances craftsmanship. In upholding these practices, artisans prepare, witness, and skillfully weave fragments of creation into holistic masterpieces.
Innovations in Rattan Cutting
In the ever-evolving landscape of rattan craftsmanship, innovations in cutting techniques are leading the way to future possibilities, merging tradition with contemporary ingenuity. These advancements are akin to opening a new act in a play, where technology becomes a new character seamlessly integrated into the narrative. Automated systems and CNC technology are transformative assets within the rattan industry, reducing waste and greatly enhancing the quality of finished pieces. Laser cutting enables precise finishes distinct to intricate designs, elevating craftsmanship without human error, honing striking consistency and execution speed.
Mobile cavity technology and optical pattern recognition systems further streamline cutting and assembly processes. The emphasis on sustainable practices reflects growing ecological awareness, with new tools requiring less energy and waste. As these innovations expand within production sites, manufacturers can anticipate fluctuations in demand without sacrificing artful integrity, benefitting both profitability and artistry.
The integration of these technologies enhances the economic viability of rattan products and fosters cultural preservation, carrying traditional practices into the contemporary marketplace with distinction and reverence for history.
Technological Advances in Cutting Equipment
Technological advances in rattan cutting are transforming production landscapes, offering techniques that enhance precision while bolstering efficiency. Within this progression, we find local implementations of CNC technology computer numerically controlled systems that encourage delicate precision at scales daunting to manual methods. These machines deliver cuts, resonating with machine orchestrators whose harmony rights perfection amidst production.
Additionally, the introduction of laser cutting techniques empowers artisans with tools rivaling traditional hand craft. These instruments can carve complex designs without the requirement of repetitive marks or preliminary sketches, cutting down on production time while securing accuracy. The continued expansion includes optical pattern systems, aligning each rattan piece to specification with an eye for detail unsurpassed in hand-measured applications.
Machine automation has reshaped production lines, enabling manufacturers to quickly navigate demand fluctuations, customizing offerings based on market trends. As such technological advances unfold, they provide convenient platforms for craftsmanship's preservation, affording artisans enhanced support.
Future Trends in Rattan Cutting Techniques
Future trends are shaping rattan cutting into more sustainable and efficient practices. With emphasis on harmonizing technology with traditional methods, the scene is set for innovations that echo ecologically conscious commitments alongside increased economic opportunity.
Precision Methods:
- Technological solutions enhance precision, enabling more accurate cuts, maintaining exceptional product quality, and encouraging sustainable lowering of material waste.
- The focus mirrors a musician's commitment to perfection, with each precise note minimize inconsistency and maximize quality.
Adoption of Sustainable Practices:
- Efficient methods for retaining plant integrity arise, reflecting growth sustainability and environmental consciousness.
- Balance between demand and ecological stewardship becomes primary, promoting environmentally conscious decisions.
Technological Integration:
- Drones and digital tools enable teams to identify and optimally harvest materials, fostering incremental improvement over time.
- Permacane technologies emerge, allowing low-quality materials to satisfy various architectural applications; innovation sees each resource achieves its highest potential.
Through these future trends, rattan cutting becomes not just a process but an opportunity to align method and mechanics in sustainable harmony. This confluence builds an ecosystem embracing ecological goals while endorsing innovative strategies and enhanced sophistication.
Sustainability in Rattan Cutting Practices
Sustainability in rattan cutting reflects a deeper commitment to responsible production, where holistic approaches intertwine ecological, economic, and cultural threads into a tapestry sewn with intention. Embracing sustainability aligns with ongoing technological innovations combining a willingness to evolve with a pledge to scars legislation and tradition, allowing rattan to offer enduring gracefulness without depleting resources.
Sustainable Harvesting:
- Techniques ensure the resource's regrowth; adopting harvests above roots supports rattan's preservation for future growth cycles.
- Balanced commercial demands become transformative agents respecting natural revival processes.
Waste Management:
- Problematic outsider waste reduction aligns with ecological and economic supervision Waste becomes managed effectively post product completion.
Community and Local Economic Development:
- Commitment to sustainable practices enhances local community engagement.
- Through frameworks protecting materials, artisanship finds new life cultivating skills while sustaining desired traditions. As environmentally-friendly markets expand, these practices speak, preserving local and cultural rattan craftsmanship.
These strategies encompass not just outputs but broader economic implications. In coupling sustainability amidst innovation congruently with cultural preservation, rattan cutting emerges as a paragon of contemporary crafting, leading forthrightly into the future.