Supply chain efficiency evaluation for rattan product manufacturers
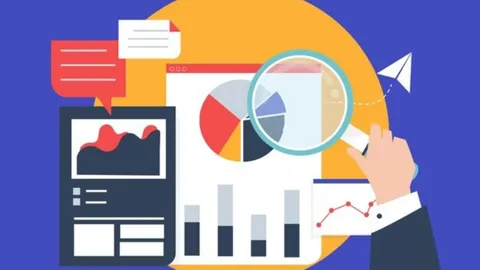
In the verdant realms of Southeast Asia, the supple vines of rattan intertwine to forge one of the world's most sustainable and versatile natural resources. The artistry of rattan manufacturing is not merely in its crafting, but also in the complex choreography of its supply chain an intricate ballet of movement, timing, and precision. As global demand for rattan products rises, manufacturers are compelled to optimize their operations to ensure consistency and quality, while balancing environmental concerns. This exploration into the world of rattan product supply chains unveils the core metrics, unique challenges, and emerging trends that shape their efficiency. Through rigorous evaluation, significant cost savings and sustainability gains can be aligned, which is essential for navigating the bustling markets and evolving consumer preferences of today and tomorrow.
Importance of supply chain efficiency in rattan manufacturing
Supply chain efficiency is a cornerstone in the rattan manufacturing industry. Imagine it as the backbone of a thriving sapling, providing both structure and flexibility. It touches on elements crucial to operational success: cost management, responsiveness, quality, customer satisfaction, and sustainability. A streamlined supply chain minimizes waste, reducing costs related to raw materials and inventory while enhancing the speed at which manufacturers can respond to market fluctuations. Diverse but specific metrics provide a lens into evaluating these efficiencies, ensuring every stage from harvest to delivery contributes towards a final product adored by customers worldwide. The metrics mentioned, such as inventory turnover ratio and cost per unit, form the toolkit by which manufacturers assess their performance, striving for an orchestrated flow akin to nature’s own symphonies.
Metrics for evaluating supply chain efficiency in rattan production
In the pursuit of supply chain efficiency, rattan manufacturers must embrace a blend of quantitative and qualitative measures. From cost-related evaluations to time-centric analyses, these metrics collectively form an integrated approach to performance assessment. Cost efficiency metrics delve into the economic aspects of production, scrutinizing expenditures to ensure resource optimization. In parallel, time efficiency metrics gauge the speed and reliability of order fulfillment, essential for keeping pace with the pulsating rhythm of demand. Quality control stands as a sentinel over product integrity, making quality metrics in supply chain performance pivotal each metric a note in the harmonious composition of the great production chain. Exploring these areas one by one, manufacturers unlock the potential to enhance operations, ensuring their creations are woven into the fabric of consumer satisfaction.
Cost efficiency metrics
The tapestry of cost efficiency metrics serves as a critical instrument in the symphony of rattan manufacturing. It is about the deft manipulation of elements such as materials, labor, and operating costs, creating a resonant chord of value against expense. A strategic focus on these metrics can empower manufacturers, unveiling opportunities for cost savings and improved profitability.
Initially, the Total Supply Chain Management Cost as a Percentage of Sales emerges as a prominent metric. Its utility lies in its ability to reveal the share of revenue absorbed by supply chain processes. This quantification enables rattan manufacturers to pinpoint inefficiencies, offering a chance to fine-tune their operations. By benchmarking against industry standards, companies can aim to lower this percentage, thus enhancing overall financial performance.
Similarly, the Supply Chain Cost per Unit Sold metric offers deep insights. By calculating the cost associated with producing each unit, from inception to sale, manufacturers can identify where greatest efficiencies can be unlocked. Higher efficiency translates to lowered costs without sacrificing quality, a feat paramount in such a competitive market.
Further, the Gross Margin Return on Investment (GMROI) metric stands as a testament to a manufacturer's ability to make prudent investment decisions. By assessing inventory against gross profit, this metric empowers manufacturers to balance stock levels enough to meet demand, not so much as to accrue excess overhead.
Lastly, Inventory Holding Cost should not be underestimated. Inclusive of storage, insurance, and spoilage expenses, this metric's reduction is emblematic of streamlined warehousing and effective inventory management.
This ensemble of cost-focused evaluations illuminates pathways to economic savings, pressing the idea that, like a skilled orchestra, each component must perform seamlessly to bring forth the budgetary harmony vital in the production of rattan goods.
Time efficiency metrics
In the ever-evolving marketplace of rattan goods, time waits for no manufacturer. Here, time efficiency metrics harmonize with industry rhythms to ensure customer satisfaction is maintained and competitive edges sharpened. They act as temporal sculptors, crafting the cadence of production and delivery to meet consumer demands swiftly and effectively.
The Customer Order Cycle Time serves as a pivotal indicator of this efficiency. By measuring the interval from order to delivery, manufacturers can gauge the swiftness with which they meet customer needs. Reducing this metric is paramount; lessened waiting times increase consumer loyalty and market reputation.
Equally vital, Lead Time reflects on the broader timeline from the origin of production to the product's arrival at its destination. Shortening lead time enhances operational flexibility, preventing bottlenecks and ensuring market readiness. It is not only internal production speed that must be streamlined but also external factors like supplier punctuality and logistical fluidity.
The Service Rate or On-time Delivery Rate adds another dimension to the time efficiency tableau. It defines the proportion of orders arriving precisely as scheduled, a tapestry of punctuality. High service rates indicate a responsive, agile supply chain a boon in any product landscape.
Lastly, the Perfect Order Index stands as the pinnacle of flawless logistic execution, measuring orders meeting exact delivery criteria, including timely and undamaged receipt, accurate specification, and complete documentation. Achieving a high percentage here speaks to a company's prowess in synchronizing each facet of its logistical mandates.
Each temporal measure serves as a vital stitch in the fabric of effectiveness for rattan manufacturers defining schedules, alleviating logistical strain, and ultimately harmonizing operations to meet the beating heart of consumer expectation.
Quality metrics in supply chain performance
The quality metrics wielded within rattan manufacturing supply chains stand as bastions of excellence, ensuring products not only meet but exceed consumer expectations. They are guardians of a company’s reputation, measuring the caliber of creations as they journey from raw material to finished product.
Leading the charge, the Perfect Order Rate metric assesses the comprehensive success of order deliveries meeting every customer-specified requirement. In an industry like rattan, where craftsmanship is paramount, maintaining a high perfect order rate builds customer trust and brand loyalty.
At its core, the Order Fill Rate illuminates the consistency and reliability of inventory management. By ensuring that customer orders are completed fully and accurately on the initial shipment, manufacturers can boost satisfaction and minimize costly backorders. This metric underscores a company's competency in balancing stock levels against unpredictable market demands.
Simultaneously, the Cost of Quality unravels the intricate layers of expenses tied to maintaining superior quality. Managing this cost efficiently is crucial for profitability striking the right balance between prevention, appraisal, and failure costs to ensure long-term viability in the competitive landscape of rattan products.
For many, Supplier Quality Performance remains a foundational component of high-quality production. It measures the dependability of materials received, offering insights on defect and rework rates. Quality begins at the source; fostering strong supplier partnerships can be key to salvaging inefficiencies in rattan input quality.
Lastly, Customer Returns numbers shed light on dissatisfaction thresholds and product reliability. Efficient handling of this metric implies faultless production cycles where returns are minimized due to the consistent quality output.
Each quality metric serves as a keystone in building a durable, reputable brand, driving the narrative that rattan manufacturers uphold material integrity throughout their supply chain endeavors leading to unrivaled consumer delight and market differentiation.
Challenges in achieving supply chain efficiency for rattan products
Despite clearly defined metrics, challenges still lie in achieving optimal supply chain efficiency for rattan products. These challenges can be likened to turbulent waters beneath a steady vessel, requiring constant vigilance and adaptation. Environmental impacts are a pressing concern, where unsustainable harvesting practices can endanger the very resources manufacturers depend on. Equally, supply chain disruptions whether from natural disasters or socio-economic upheaval pose substantial risks. Managing such upheavals requires strategic resilience planning and flexibility.
Environmental impacts of rattan supply chains
The environmental impacts of rattan supply chains are both profound and potentially destructive, compelling manufacturers to embody sustainable practices. Picture a landscape burdened by relentless harvesting, with ecosystems teetering on a delicate edge. As rattan is extracted from tropical forests, overharvesting risks not only deforestation but the disintegration of local biodiversity a tapestry unraveled by shortsighted practices.
Deforestation is a leading concern, with unsustained extraction practices harming vital ecosystems. The continued degradation of these environments stresses the urgent need for responsible sourcing, where regenerative practices such as reforestation must mend the ecological fabric.
The reverberations of habitat loss are echoed across flora and fauna populations, where each vine uprooted without foresight disrupts a symbiotic balance. Biodiversity suffers as animal habitats shrink and plant species dwindle, underscoring the importance of sustainability.
Manufacturers can spearhead initiatives that prioritize eco-friendly practices within their supply chain operations. These include encouraging sustainable harvesting methods, reducing production waste, and investing in environmentally conscious packaging. An investment in conserving natural resources translates to long-term viability.
Moreover, climate change looms as an abstract antagonist, altering weather patterns in rattan-producing regions. Floods and storms can devastate supply chain infrastructure, necessitating forward-thinking strategies to mitigate these forces.
Ultimately, addressing environmental impacts means reframing the supply chain from a linear path of consumption to a circular cycle of renewal ensuring that each rattan pole harvested is not an end but a beginning. In doing so, manufacturers not only safeguard their supply chains but contribute to the preservation of our planet's precious biodiversity.
Supply chain disruptions and their effects on rattan manufacturers
Supply chain disruptions ripple through the fabric of rattan manufacturing, akin to tremors that unsettle even the most stable of edifices. They manifest unpredictably, whether by stark global events or local crises, necessitating agility and foresight to navigate their turbulent wake.
Global disruptions, such as the COVID-19 pandemic, showcase the fragility of interconnected supply networks. For rattan manufacturers, such disruptions translate into obstacles reduced production capacity, logistical delays, and increased operational costs. Navigating these uncertainties requires strategic contingency planning and diversified sourcing strategies.
Environmental disruptions often compound the complexity of the supply chain, where natural disasters like floods and fires can halt operations abruptly. The solution lies in building resilience through geographical diversification of suppliers and reinforcing lines of communication.
Moreover, political instability in rattan-producing regions presents another layer of challenge. Tariffs, trade restrictions, and regulatory changes can disrupt supply chains, making flexibility key. Developing multi-level supplier relationships and maintaining in-region expertise can help mitigate these risks.
Demand fluctuations can be equally disconcerting. Rattan products are subject to variable consumer preferences, influenced by trends towards eco-friendliness. Manufacturers must leverage data analytics for precise demand forecasting to balance stock levels confidently and avoid costly overproduction.
In essence, bolstering supply chain resilience becomes the cornerstone of enduring disruptions. This involves proactive strategies, including investing in technology to enhance supply chain visibility and instituting robust risk management frameworks ensuring manufacturers withstand the test of unforeseen challenges.
Best practices for enhancing supply chain efficiency in rattan manufacturing
To thrive in the rattan industry, manufacturers must adopt best practices that enhance supply chain efficiency. These are the pillars of stability, supporting operations in the face of challenges highlighted earlier. As industries evolve, automation, innovative supplier relationships, and collaborative strategies have become guiding stars for those aiming to optimize their processes without sacrificing quality or compromise principles.
Automation in rattan product supply chains
In embracing automation, rattan product supply chains can transcend traditional limitations, stepping into a modern era where precision meets productivity. Automation imbues every production stage with efficiency, akin to infusing a symphony with sophisticated orchestration.
Smart manufacturing technologies serve as the backbone of automated rattan supply chains. Employing Internet of Things (IoT) systems and robotics, manufacturers can achieve real-time monitoring and adaptation creating a seamless synchrony between consumer demands and production output.
By integrating machine learning algorithms, manufacturers gain insight into market trends and operations optimization, enabling them to anticipate changes and respond with acuity. The potential to fine-tune processes and minimize errors results in cost reductions and enhanced product quality, conveying value to end-users.
Automated inventory management systems reduce the complexity of stock handling. From warehousing to fulfillment, the processes become streamlined with immediate order processing and efficient replenishment ensuring customer demands are met without delay.
Automation not only increases production speed but harmonizes operational flows, aligning them with the dynamic demands of a global marketplace. The rattan industry, often steeped in tradition, can flourish anew through these innovations revolutionizing how goods are crafted, managed, and delivered.
Importance of supplier relationships for rattan efficiency
The success of a rattan supply chain is magnified by the importance of supplier relationships, akin to the reliable friendships that fortify community bonds. Healthy supplier relations foster trust, innovation, and cost-efficiency, creating a backbone of reliability upon which a manufacturer can rely.
Through consistent collaboration, manufacturers and suppliers can achieve synchronized quality improvement efforts addressing inconsistencies, enhancing material reliability, and jointly developing solutions to production challenges. A robust partnership breeds loyalty, enhancing continuity even in volatile markets.
Cost savings are also inherent in well-managed supplier partnerships. Manufacturers can negotiate favorable terms, resulting in mutually beneficial economic arrangements. This fosters a competitive edge within the market, reducing operational expenditures and driving profitability.
Moreover, fostering supply chain resilience is an additional boon of supplier relationships. By sharing insights and strategies, manufacturers and suppliers can create adaptive supply chains capable of weathering disruptions. Each partner contributes unique value, augmenting the capacity for collective problem-solving.
In pursuing innovation, the value of close supplier ties becomes even clearer. Manufacturers have access to cutting-edge technologies and methodologies, surmounting barriers to entry that might otherwise limit market differentiation. These synergies propel rattan product trade forward, encapsulating productivity, creativity, and efficiency.
In summary, deepening supplier engagement enriches the rattan supply chain, fostering collaboration that permeates each facet of production. This results in a milieu where both efficiency and innovation can flourish unbounded ensuring the rattan industry remains a bastion of quality and sustainability in the natural product sphere.
Comparison of supply chain efficiency in rattan versus other natural products
When juxtaposed against other natural products like bamboo or wood, rattan's supply chain efficiency presents unique characteristics. Rattan's specificity emerges as a defining trait due to its reliance on particular geographic locales for sourcing, setting it apart from more ubiquitously sourced materials. This dependency can precipitate vulnerabilities less pronounced in materials like bamboo, which enjoys a wider distribution network.
Market demand for rattan is closely tied to environmental awareness and the shift towards natural aesthetics. By maintaining strong supplier relationships, rattan manufacturers may exercise greater agility in adapting to consumer preferences compared to those with less integrated supply systems.
Cost-wise, rattan can indeed be economically favorable, given its lower production costs when effectively managed. However, inefficiencies can erase such advantages if supply chain management lacks diligence. Hence, strategic partnerships are crucial to leverage cost-effectiveness against competitors in the natural product realm.
Innovation capabilities also distinguish rattan. Manufacturers who cultivate effective supplier bonds can more readily pursue design advancements and novel processing techniques. This innovative edge allows rattan to surpass other natural materials in versatility and application, providing bespoke solutions tailored to current trends and consumer feedback.
Ultimately, the nuanced interplay between supplier management, cost efficiency, and eco-from also crucial in aging markets demonstrates the capabilities of building blocks of a highly proficient rattan supply chain are critical unicity innovation that allows it to withstand external fluctuations. these dynamics put rattan in a peerless position.
Case studies on successful supply chain efficiency improvements in rattan manufacturing
Exploring case studies offers tangible insights into successful supply chain efficiency improvements in rattan manufacturing. Permacane's technological progression exemplifies how technological adaptation has expanded rattan's utility in furniture and design. By optimizing resource usage, energy efficiency has blossomed, with waste slashed significantly from 80% to a minimalist effect. This approach is a testament to what streamlined supply chains in rattan manufacturing are capable of.
Meanwhile, global examples include a large retail chain coalescing efforts in collaborative sourcing strategies. The ability to jointly purchase key commodities allowed them to achieve notable cost reductions, offering a beacon for similar pursuits across rattan industries. This collaboration underscores the power of mutual gains and efficient resource allocation, showing that simple efficiencies can have dramatic impacts.
A beverage manufacturer's partnership with retailers in demand forecasting resonates with rattan markets. Data sharing allowed them to cut inventory levels by a third, reducing volatility. Effectively, these strategies align with rattan manufacturers, adapting to market changes with agility and foresight.
These case studies showcase the innovative potential within rattan manufacturing. By capitalizing on technologies, embracing collaboration, and predicating operations on sustainability, these success stories bear lessons that elevate the industry as a whole.
Future trends in supply chain efficiency for rattan products
As the future beckons, several trends will sculpt supply chain efficiency for rattan products, underscoring the harmony between technology and nature. The push towards sustainability stands unyielded, with more manufacturers compelled to align with ecological mandates. Sustainable practices and transparency in operations offer pathways to enhance brand perception, improve regulatory compliance, and unify market diversity.
Technological innovations are anticipated to further transform the supply chain landscape. As machine learning and data analytics gain traction, they offer improved forecasting, operational streamlining, and reduced costs. Coupled with global demand surges, these technologies equip manufacturers to expand their capabilities beyond current confines.
Moreover, enhanced collaboration between manufacturers, suppliers, and retailers will grow, promoting efficiency and mutual advancements. This incentivizes shared innovation, lowering supply chain costs and enhancing product flow. As manufacturers actively engage with retailers, efficiency is augmented, seamlessly aligning goals and feedback loops to meet consumer expectations.
Digital trends such as automation and a focus on circular economies offer enhanced opportunities. Rattan manufacturers might increasingly view these technological disruptions not as threats, but as avenues for digital transformation evolving supply chains to be agile, resilient, and adaptive.
By 2030, these trends will have refined supply chains, fostering nimbleness, sustainability, and business acumen as they aesthetically enhance spaces globally.
Impact of technology on rattan supply chains
Much has been written about the impact of technology on modern supply chains, and for rattan, this is no different. The integration of tech creates cascading effects, transforming traditional pathways into digital highways of productivity and responsiveness.
The rise of AI and machine learning imbues supply chains with a new layer of predictiveness. Manufacturers can preempt disruptions before they manifest, optimize logistics, and ensure uninterrupted production. Such foresight streamlines transitions, reducing friction points in the delivery process.
IoT applications further augment supply chain visibility. These interconnected systems allow for real-time monitoring, drawing accurate data that informs decision-making. Essential to operational management, it ensures assets are tracked, inventory managed, and inefficiencies promptly addressed.
Automation brings factories to life with a symphony of synchronized mechanisms each process a cog in a seamlessly operating machine. From weaving to packaging, automation streamlines processes, lowering error margins and human resource costs while maximizing output and maintaining consistency in quality.
Software solutions decentralize many layers of production management. Real-time data dashboards offer a panoramic view of supply chain operations from product inception to distribution, ensuring manufacturers access the critical insights needed for informed actions.
As technology continues its relentless advance, it integrates increasingly with natural product supply chains, including rattan. Through digitization, manufacturers not only stay relevant but expand their operational vision, emerging more robust, capable, and future-ready.
Sustainability practices in rattan product supply chains
Sustainability is not a passing phase but an inherent value woven into the tapestry of rattan supply chains. The movement toward sustainable practices involves understanding the reverberations of extracting, manufacturing, and distributing rattan_goods within environmental constraints.
Commitments to responsible sourcing are central. Enforcing sustainable harvesting replaces exploitative techniques with practices that ensure reforestation and biodiversity respect. This guards against deforestation’s adverse effects and builds favor among environmentally conscious consumers.
In manufacturing, practices pivot towards minimizing waste. From reducing emissions to favoring eco-friendly materials and processes, manufacturers are reshaping entire chains to reflect ecological consciousness. This transformation broadens appeal and supports adherence to global environmental standards.
Rattan manufacturers increasingly underscore transparency, heightened through supply chain visibility and accountable policies. This aligns sustainability goals with consumer demand for seamless practices, promoting cleaner production methods and investigative inventory oversight.
The incorporation of circular economy principles fosters closed-loop supply chains. By promoting recycling and reuse, material costs are trimmed, preserving the environment while maximizing earnings.
Ingraining these sustainable pillars in rattan supply chains is more than a reaction to market pressures it is a mandate promising future longevity, social responsibility, and operational excellence.
Conclusion
In assessing and improving the supply chain efficiency of rattan product manufacturers, a confluence of metrics, practices, and innovations offers pathways towards sustainable success. The intersection of cost, time, and quality metrics serves as the bedrock for understanding and enhancing supply chain operations. Facing challenges such as environmental impacts and disruptions, manufacturers are encouraged to adopt best practices and leverage automation, technology, and supplier relationships to achieve strategic efficiency.
Looking forward, the emergence of sustainability practices and technological integration promises to revolutionize rattan supply chains. As these trends unfold, the rattan industry stands well-positioned to capture an expanding market while safeguarding the ecological integrity of its source. Ultimately, the woven journey from raw material to artistry embodies the delicate dance of strategy and craft a testament to the evolving art of supply chain management in rattan manufacturing.