The Future of Customization: 3D Scanning for Bespoke Rattan Furniture
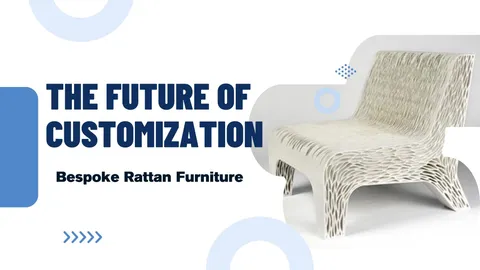
Imagine a world where furniture seamlessly integrates with the uniqueness of your home, echoing your personal style with unparalleled precision. The bespoke craft of rattan furniture, known for its intricate patterns and organic feel, is taking a futuristic leap with the integration of 3D scanning technology. As we delve into this transformative synergy, we explore how this cutting-edge technology is reshaping the landscape of custom furniture design. This convergence offers a tantalizing glimpse into the future, where artisans can capture minute details otherwise impossible, thus elevating craftsmanship to a level that marries heritage with innovation. As you embark on this journey with us, discover how 3D scanning not only enhances aesthetic appeal but also ensures structural integrity, solving age-old challenges in customization. Welcome to the future of furniture design, where your vision becomes reality through the lens of technological advancement.
The Role of 3D Scanning in Custom Furniture Design
In today’s design ecosystem, 3D scanning technology serves as an indispensable tool in custom furniture design, particularly in the realm of rattan furniture. As we navigate the shifts from traditional craftsmanship to technologically-enhanced artistry, this tool plays a pivotal role in redefining design processes. The essence of capturing precise details and measurements empowers designers with unprecedented accuracy, ensuring that every rattan piece fits perfectly into its intended environment. This capability is especially crucial for complex shapes and patterns typical of rattan furniture. Moving beyond the limits of manual methods, 3D scanning offers a myriad of benefits such as rapid prototyping, customization capabilities, and quality control, all tailored to meet specific client demands. These advantages will be delved into as we explore the transformative applications of 3D scanning across various aspects of furniture production.
Benefits of 3D Scanning Technology for Rattan Furniture
The benefits of 3D scanning technology in creating bespoke rattan furniture are profound and multifaceted. At its core, this technology enables unparalleled precision that transforms not only the design phase but also the end product's integrity and artistry. Imagine witnessing a furniture piece that mirrors its digital blueprint with astonishing accuracy this is the reality 3D scanning facilitates.
Firstly, precision measurement stands as a hallmark of 3D scanning. Traditional methods often falter in capturing the intricacies and geometric complexities of rattan patterns, where even a slight deviation can detract from its aesthetic appeal. With 3D scanning, detailed and accurate measurements create a digital model that becomes the backbone of the design process. This precision ensures that each bespoke piece adheres strictly to the client's spatial and design preferences, maintaining the artifact's intended artistry.
Moreover, rapid prototyping becomes seamlessly integrated into the workflow. Designers are no longer bound by the lengthy and costly traditional prototyping, where each iteration meant more resources and time. Instead, digital prototypes can be iterated swiftly, allowing designers to explore a plethora of configurations and styles before committing to production. This agility not only reduces time and cost but also unlocks creative potential unfathomable through traditional methods.
In addition to design improvements, 3D scanning facilitates mass customization where each furniture piece can reflect individual specifications and tastes. This capability is of particular significance in the rattan industry, where consumers often seek custom styles that harmonize with their personal space and identity. By digitally capturing precise data, designers and manufacturers can tailor every piece to meet these unique demands, ensuring a harmonious blend of tradition and personal expression.
Furthermore, the replication and restoration processes benefit immensely from 3D scanning. Consider the challenge of replicating an intricate rattan pattern developed decades ago, where fading craftsmanship poses barriers to accurate replication. 3D scanning bridges this gap by capturing every nuance of existing designs, enabling artisans to replicate them with exacting detail. This ensures heritage patterns are preserved and revitalized for future generations, safeguarding the cultural essence within modern design dynamics.
Benefits Summary:
- Precision Measurement: Accurate capturing of intricate patterns and dimensions.
- Rapid Prototyping: Swift iteration and testing of designs, reducing costs.
- Mass Customization: Tailoring pieces to individual tastes and specifications.
- Replication and Restoration: Preserving and reinvigorating intricate historic designs.
In conclusion, the integration of 3D scanning technology in rattan furniture design yields numerous benefits that enhance both the quality and customization of the final product. This synergy of tradition and innovation heralds a new era in furniture craftsmanship, where each piece not only serves a function but also tells a personalized story.
How 3D Scanning Enhances Design Flexibility in Customization
The vast potential of 3D scanning technology lies in its ability to enhance design flexibility, which is particularly transformative in the realm of custom furniture, especially rattan. It empowers designers to navigate new creative possibilities, offering tools that transcend the confines of conventional handcrafted techniques.
Consider this technology as an artist's palette, providing endless hues for creative exploration. Designers armed with 3D scanning can capture and manipulate intricate designs with the ease of a brush stroke, crafting pieces that are not only aesthetically dazzling but also structurally sound.
Design flexibility is significantly enriched through the capacity to manipulate and modify digital models. In the context of rattan furniture, where aesthetic and functional harmony is paramount, this adaptability is crucial. With a digital model capturing the precise dimensions of a given space, designers can experiment with novel designs, producing pieces that are tailored specifically to meet unique client preferences.
Key Aspects of Design Flexibility:
- Expansive Design Iterations: Experimentation with a wider variety of shapes and styles without committing to physical prototypes.
- Customization Based on Space Requirements: Tailoring designs to fit seamlessly within designated spaces, ensuring they complement existing decor.
- Collaboration through Virtual Reality: Offering clients immersive virtual experiences to view and interact with potential designs in their own space, further refining concepts based on real-time feedback.
This digital integration enables a level of customization that is unparalleled, paying homage to the personal narratives that bespoke furniture pieces often represent. With 3D scanning, designers can align aesthetic integrity with client vision more closely, creating pieces that are as functional as they are uniquely expressive.
The implications of such flexibility are further magnified when considering the speed and efficiency imparted by 3D scanning technology. With CAD software, digital models can be fine-tuned in a fraction of the time that manual adjustments would require, leading to faster decision-making and reduced time-to-market.
In a world where interior aesthetics often serve as an extension of personal identity, the demand for bespoke rattan furniture reflects an increasingly discerning clientele. This segment benefits notably from 3D scanning, which allows offerings to be more uniquely personalized, catering to individual tastes and preferences. Through technology, the craftsmanship of rattan furniture is elevated, creating a symphony of design possibilities that encompasses both form and function with exquisite balance.
In essence, the push towards 3D scanning in furniture design opens up a realm of inventive potential that was previously limited by traditional methodologies. It allows design to transcend mere function, evolving into an art form that is both captivating and deeply personal, offering an exciting vision for the future of home furnishing customization.
Applications of 3D Scanning in the Production of Rattan Furniture
The incorporation of 3D scanning technology into the manufacturing of rattan furniture has marked a revolutionary shift, enhancing both efficiency and creativity in the production process. As furniture design transcends traditional boundaries, the applications of 3D scanning range from initial design to quality assurance, each phase benefitting significantly from its precision and agility.
The transition from traditional design methods to modern digital processes allows for an exciting expansion of possibilities for both designers and manufacturers. This section will delve into how these advancements enable seamless integration across various facets of rattan furniture production, laying the groundwork for subsequent discussions on quality control and manufacturing processes.
Integration of 3D Scanning in Manufacturing Processes
Integrating 3D scanning technology within the manufacturing processes of rattan furniture offers transformative benefits, introducing a new paradigm of efficiency and precision that resonates through every stage of production. This integration is comparable to trading a handwritten map for GPS navigation; it forever alters the way manufacturers approach the production landscape.
From the outset, the design and prototyping stage undergo significant evolution. Traditional prototype development methods involved numerous iterations, which were time-consuming and costly, often leading to resource waste. In contrast, 3D scanning technology allows for high-fidelity digital models to be produced first, paving the way for rapid prototyping. This means designers can tweak and perfect a design virtually before investing time and materials into creating a physical version. The technology captures the intricate artistry of rattan, ensuring that the aesthetic integrity of each piece is preserved, a feature crucial to its charm and appeal.
Some key benefits of integrating 3D scanning into manufacturing include:
- Efficiency in Design Modifications: In a digital realm, designs can be effortlessly modified and adjusted, providing flexibility and reducing lead times from concept to completion.
- Waste Reduction: By optimizing material use and reducing trial-and-error methods in physical prototyping, manufacturers achieve significant material savings.
- Preservation of Artistry: The exactitude in capturing complex designs maintains the distinctive, organic aesthetics that rattan is known for, blending tradition with modern innovation.
Customization, a cornerstone of furniture design, is also significantly enhanced. The high demand for bespoke furniture results from consumers' desire for pieces that reflect their distinct taste and fit specific spaces. 3D scanning facilitates this by enabling manufacturers to quickly adapt pre-existing designs or create new ones based on consumer-demanded specifications. This agility not only satisfies the desire for unique products but also boosts customer satisfaction by providing tailored solutions.
Thus, 3D scanning acts as a liaison between aesthetic imagination and tangible creation, offering a more efficient pathway to achieving customer needs.
Moreover, the potential applications extend beyond mere production efficiency; they usher in a new era of collaboration between traditional craftsmanship and digital innovation. By embracing 3D scanning technology, rattan furniture manufacturers not only amplify production capabilities but also honor the timeless artistry that defines their craft, ensuring that each piece delivers both function and beauty to perfection.
Ensuring Quality Control with 3D Scanning Precision
In the intricacies of rattan furniture production, where each weave and detail contributes to the overall beauty, ensuring quality control is of utmost importance. 3D scanning technology provides a precise mechanism that enhances quality assurance protocols, enabling manufacturers to maintain consistency and excellence from the first scan to the final product.
Much like a conductor ensuring each instrument plays in harmony, 3D scanning orchestrates the perfect balance between design and functionality, ensuring each component meets strict geometrical specifications. Implementing high-precision measurement tools means that no detail is too small to escape scrutiny a critical aspect considering the structural and aesthetic demands of rattan furniture.
Key Elements of Quality Control Enhanced by 3D Scanning:
- Precision Measurement: The technology provides accurate scanning and evaluation of complex geometric forms, crucial for the integrity and assembly of rattan furniture components.
- Feedback Loop Creation: Real-time feedback from integrated systems helps modify production processes instantly to correct deviations from design, preventing costly errors and ensuring the highest quality standards.
- Non-Contact Inspection: The innovative non-contact method eliminates manual error, allowing for rigorous testing without affecting the product’s surface quality.
For manufacturers, adopting ISO 10360-08 standards ensures devices used for scanning maintain their precision, which is essential to quality control in rattan furniture production. The integration forms a backbone to the production line, where every piece is measured against original specifications, assuring consumers get exactly what was promised in both design and durability.
By stabilizing these control mechanisms, 3D scanning adds value beyond aesthetics, offering structural integrity and reliability in each crafted piece. This technological advancement doesn't just streamline production processes but further enhances reputation in consistency and dependability.
In every curve, twist, and weave, the eye of a discerning artisan magnified through the lens of 3D scanning ensures that each rattan furniture piece not only meets the occupational standards but also exceeds the artistic expectations of a variety of bespoke requests. Thus, it solidifies its place as an indispensable tool in modern furniture manufacturing, harmonizing age-old craftsmanship with the precision of digital technology in a beautiful dance of innovation.
Comparing Traditional Furniture Design with 3D Scanned Customization
In comparing traditional furniture design with customization enabled by 3D scanning, stark differences emerge not just in methods but also in the possibilities each approach unlocks. Traditional methods, while rooted in nostalgia and craftsmanship, often struggle under the weight of modern demands for precision, speed, and customization. On the other hand, 3D scanned customization propels furniture design into a realm where innovative possibilities flourish, offering a more precise, efficient path from concept to creation.
Examining these facets gives us a clearer understanding of how 3D scanning stands to redefine the future of furniture design, marrying craftsmanship with state-of-the-art technology seamlessly.
Customization Capabilities: Traditional Methods vs. 3D Scanning
Traditional methods in furniture customization are revered for their artistry but often fall short in flexibility and expedience. Typically, customization under these methods involves a time-intensive process relying heavily on skilled craftsmen to manually tweak designs a process akin to painting a mural with a delicate brush across vast canvases blanketed with intricate details. This approach, despite its artistic value, poses significant limitations especially when faced with bespoke creations that require precision and repeatability.
Conversely, 3D scanning circumvents these constraints, offering an avenue where every detail is captured swiftly and accurately, akin to composing digital symphonies from physical inspirations. Here’s how these two approaches differ:
Traditional Customization:
- Time Consumption: Extensive manual adjustments lead to prolonged timelines for project completion.
- Resource Intensity: High demand for skilled labor and material use, driving up costs.
- Limited Customization: Constrained by manual execution, intricate designs face challenges, often resulting in compromising client vision for feasibility.
- Inconsistencies: Variability across crafted pieces due to artisanal discrepancies.
3D Scanned Customization:
- Speed and Efficiency: Rapid model adjustments and iterations create pathways to accelerated production timelines.
- Cost Effectiveness: Less reliance on raw materials and physical prototyping reduces overhead and waste.
- Enhanced Personalization: The capability to alter digital models allows for an expansive range of bespoke designs aligned precisely with client specifications.
- Consistency Across Production: Computer-controlled processes deliver uniformity in design outcomes, ensuring predictably high-quality products.
The advent of 3D scanning in furniture design bridges the gap between consumer demand for distinct pieces and the producer’s ability to deliver exquisite craftsmanship without compromise. As artistic directors of their home aesthetics, consumers are no longer bound by rigid production timelines or standard designs; instead, they find themselves empowered by readily available, precisely tailored options that reflect personal tastes effortlessly.
As furniture evolves from simple functional constructs to multifaceted expressions of individuality within homes, 3D scanned customization operates as a transformative force in the industry. It steers us towards a paradigm where each custom piece serves as not only a utilitarian asset but also a narrative infused with individuality and style, woven digitally but materialized traditionally, showcasing how technology can breathe modernity into ancient craft.
Cost Implications of 3D Scanning for Bespoke Rattan Furniture
Navigating the cost implications of adopting 3D scanning for bespoke rattan furniture unveils layers of potential savings and investments. Traditional furniture design, while steeped in artisan legacy, frequently involves inefficiencies and associated financial burdens. Material wastage and extensive labor requirements contribute to the costs, making the crafting of each piece economically daunting.
In the juxtaposition, 3D scanning technology emerges as a beacon of economic efficiency. This technology introduces a paradigm shift across several cost-driving factors:
- Reduced Material Waste: Traditional methods, relying on physical raw material prototyping, often entail significant material waste an inefficiency largely eliminated by 3D scanning. Precise digital designs allow for optimized use of materials, reducing waste substantially and translating into direct cost savings.
- Labor Cost Reduction: The automation of replication and design alteration in the digital realm minimizes manual labor, cutting expenses significantly.
To add perspective, consider the economic layout of these two approaches:
Aspect
Traditional Design ($)
3D Scanned Customization ($)
*Material Waste**
High
Low
*Labor Intensity**
High
Moderate
*Prototyping Costs**
High
Minimal
*Design Iterations and Customization Options**
Limited
Expansive
Beyond direct cost considerations, 3D scanning also opens avenues for added value through flexibility in design, enhancing consumer satisfaction and allowing the exploration of complex forms previously constrained by cost. Consumers are more engaged, often willing to invest more in tailored solutions that meet their exact needs without compromising on design integrity or timeline demands.
In future trends, the fusion of 3D scanning with other technologies such as 3D printing is expected to further disrupt cost structures, allowing a broader spectrum of material possibilities and reducing waste significantly. This alliance promises intricate designs that are not only aesthetically alluring but also economically sensible.
Furthermore, with growing awareness around sustainability, consumers are gravitating towards eco-friendly practices. 3D scanning allies with sustainable goals by minimizing waste, optimizing material efficiency, and cutting the carbon footprint associated with traditional manufacturing methods.
In summary, the cost implications of integrating 3D scanning for bespoke rattan furniture lean favorably towards economic prudence without forgoing quality or creativity, paving a promising path for future customization trends focused on efficiency and innovation.
Future Trends in 3D Scanning and Furniture Customization
In the landscape of furniture design, the conversation surrounding the future is vibrant with possibilities spurred by 3D scanning and customization practices. As this dialogue unfolds into practical applications, a new frontier emerges where the boundaries of creativity and functionality expand exponentially. Building on the foundation laid by comparing traditional and scanned methods, we explore groundbreaking innovations driving this transformation as well as the embrace of sustainable practices, setting the stage for a future where customization caters to both aesthetic and environmental sensibilities.
Innovations Driving 3D Scanning Technology Forward
With the advent of technological advancements, 3D scanning technology is evolving swiftly, enhancing customization capabilities, particularly for rattan furniture. These innovations are akin to a symphony, each note representing precision, speed, and user accessibility, collaborating in harmony to orchestrate bespoke furniture design.
Key Innovations Include:
- Improved Accuracy and Speed: Modern 3D scanners, characterized by advanced algorithms, capture intricate data with unprecedented accuracy and speed. This efficiency empowers designers to iteratively refine designs based on client feedback without substantial time delays, a leap forward akin to advancing from sketches to digital blueprints overnight.
- Seamless Integration: The harmonization of 3D scanning with CAD software presents a seamless interface for translating scanned objects into digital models. This fluidity enhances rapid prototyping and substantial customization aligned with client predispositions, supporting creativity while being anchored in digital precision.
- Affordable and Portable Devices: The proliferation of budget-friendly, compact scanning devices democratizes this technology. Furniture makers, from fledgling artisans to industry veterans, can adopt 3D scanning to craft custom designs efficiently, expanding the bespoke market without significant capital investment.
- User-Friendly Interfaces: Intuitive software interfaces empower even those with limited technical expertise to navigate 3D scanning technology effectively, reducing the learning curve and enabling more stakeholders to engage in the customization process innovatively.
These technological advancements lay the groundwork for future trends, transforming the customization landscape for industries such as that of bespoke rattan furniture, propelling art into the digital age and tailoring creative expression in unprecedented ways.
Impact of Sustainable Practices on Custom Rattan Furniture Through 3D Scanning
Sustainability in furniture design is no longer just a supplementary consideration but a pivotal influencer in customizing future trends. 3D scanning significantly contributes to this sustainable design ethos, providing tools and processes that align environmental consciousness with customization demands.
Consider a canvas where each stroke is measured not only for its beauty but also for its impact on the environment. 3D scanning catalyzes this perspective, crafting designs that are both pleasing to the eye and mindful of ecological footprints.
Impact Highlights:
- Material Efficiency: By allowing precise measurement, 3D scanning optimizes rattan use, reducing waste significantly. Accurate assessments of material needs ensure conservation efforts, turning sustainability from aspiration into operational practice.
- Lifecycle Assessment: Incorporating this technology from the design phase facilitates comprehensive lifecycle assessments. Designers can visualize and quantify the environmental impact of their products, enabling informed decisions that promote sustainability pragmatically.
- Enhanced Durability and Longevity: Designs informed by precise scanned data lead to better construction practices, ensuring the aesthetic appeal is matched by structural integrity. Improved durability translates to fewer replacements, reflecting a commitment to long-term sustainability.
The impact of 3D scanning technology is profound, not merely as a toolset for design but as a catalyst cementing sustainability in the core values of custom furniture design. This evolution sets the stage for an era where consumer desires for personalization blend seamlessly with ecological stewardship, redefining the narrative of bespoke furniture. In this light, 3D scanning emerges as not only a technological asset but also a symbol for sustainable innovation, enabling designs that echo with both personal expression and global responsibility.
Challenges in Adopting 3D Scanning for Rattan Furniture Customization
The journey towards integrating 3D scanning technology in rattan furniture customization, while promising, is punctuated by recognizable challenges. As we venture beyond the advancements and sustainable potential of this technology, we encounter specific hurdles, particularly technical limitations, that necessitate innovative solutions. These challenges, akin to navigating amid the finesse of delicate craftsmanship and the precision required by digital modalities, define the transition pathway and guide the industry towards overcoming adoption barriers in gaining consumer trust.
Technical Limitations and Solutions in 3D Scanning
Challenges associated with adopting 3D scanning for rattan furniture often revolve around the interplay between organic materials and digital capture methods. Rattan’s natural, intricate patterns, combined with its surface characteristics, pose particular challenges that scanning technologies must navigate diligently.
Relevant Challenges Include:
- Material Characteristics: The fibrous, flexible nature of rattan alongside color variations presents issues for accurate scanning. Traditional 3D scanners may struggle with these surfaces, leading to potential data inaccuracies and detail loss.
- Surface Texture and Finish: For furniture where texture significantly contributes to visual and tactile aesthetics, inadequacies in scanning equipment may result in losing finer details in the digital model an essential component in design processes.
- Complex Geometries: Rattan's natural bends and curves require advanced scanning technologies like laser or structured light scanning to ensure precise detail capture, often challenging for equipment optimized on more symmetric forms.
Solutions to Navigate these Challenges:
- Advanced Scanning Technologies: Embracing higher-resolution scanners or hybrid technologies that combine 3D scans with photogrammetry can capture intricate detail and maintain the integrity of complex geometries presented by rattan structures.
- Optimized Conditions: Controlling environmental conditions such as lighting and surface reflections prior to scanning can significantly enhance data accuracy, ensuring a stable environment to mitigate variability impacts.
- Post-Processing Expertise: Utilizing sophisticated post-processing software to refine captured data enhances detail preservation and model fidelity, employing techniques such as noise filtering for optimal digital renditions.
- Training and Education: Educating operators in specific nuances of 3D scanning for materials like rattan fosters better data acquisitions strategies, driving higher accuracy and reliable outcomes.
Investing in comprehensive solutions and proactive strategies transforms these challenges into opportunities, steering the introductory phase towards smoother integration within the furniture design process. These resolutions draw from both technological advancements and practical adaptations, indicating broader acceptance and successful integration into the industry's ecosystem.
Addressing Consumer Perceptions of 3D Scanned Products
Adoption challenges transcend technical aspects, encompassing consumer perception and acceptance issues vital to expanding 3D scanning in furniture customization. Central to this challenge is the privacy paradox rooted in emerging technologies such as 3D body scanning. Concerns around data privacy, accuracy, and usability significantly influence consumers’ willingness to embrace 3D scanned customizations, highlighting a nuanced area requiring strategic focus.
Addressing these challenges calls for a collective understanding and communication initiative regarding 3D scanning’s value-add to customization:
- Privacy Concerns: Consumers often express anxiety over personal data collection involved in scanning processes. Proactively addressing data security concerns, enhancing transparency around usage, and ensuring compliance with data protection regulations can alleviate these fears and bolster trust.
- Accuracy and Detail Representation: For rattan furniture, the inability to capture intricate patterns and execute ergonomic needs effectively may dampen consumer confidence. Advancements in scanner resolution and software improvements promise enhanced accuracy, bridging these gaps and delivering designs that meet custom specifications reliably.
- Consumer Fit and Ergonomics: A popular challenge with 3D scanning often lies in its perceived rigidity in customizing individual user preferences effectively. Demonstrating the flexibility and personalization capability of scanned designs, especially in ergonomic fit, can drive acceptance and preference for scanned products.
Ultimately, through articulate communications and strategic consumer education, the barriers surrounding data privacy, accuracy, and customization in 3D scanned designs can be diminished. This fosters an environment where technology adoption is not only feasible but preferable, translating into broader industry transformations and paving the way for informed, discerning consumers who appreciate the union of innovation and individuality offered by bespoke rattan furniture designed via 3D scanning technology.
Conclusion
The integration of 3D scanning into furniture design, particularly within the realm of bespoke rattan pieces, represents a significant stride into the future of customization. This transformative technology bridges tradition and modern innovation, advancing the bespoke industry by enhancing precision, flexibility, and sustainability. As automation reshapes design landscapes, aesthetic integrity and individualized expression emerge as key narratives, mirrored in every intricately designed piece. The journey, while filled with complexities and challenges, indicates the potential to redefine craftsmanship through digital lenses, ensuring unique, personalized furniture not only meets but exceeds consumer expectations. Therefore, embracing 3D scanning isn’t merely about adopting new technology; it's about casting a vision for a future where each detail, weave, and nuance is harmonized with consumer desires and sustainable aspirations, marking an indelible journey from artistry’s past to its promising digital future.